The Influence of Different Arrangements of Shallow Dimples on the Resistance of Plates Subjected to Relative Fluid Motion
DOI:
https://doi.org/10.24352/UB.OVGU-2019-005Abstract
Shallow dimples have long been a scientifically investigated topic to reduce the flow resistance of objects subjected to overflow. Most of the investigations on the influence of dimples on flow resistance have so far been carried out experimentally. Although the arrangements and flow conditions are often similar, different research activities conclude differently concerning the effect of the surface structures. This also leads to disagreement regarding the causes of flow resistance reductions. In this paper, time-resolved Large Eddy Simulations on two different, already experimentally investigated setups of dimples have been carried out to better understand the effects of dimples on the surface being subjected to relative fluid motion. In one case the dimples were examined in overlapping arrangement, in the other case in a non-overlapping arrangement. We were able to show that the formation of streaks near the surface significantly influences the local contribution to the flow resistance. For the overlapping arrangement, only a slight resistance reduction of 0.12% was determined. For the non-overlapping arrangement, the mean resistance reduction was found to be 3.16%. Regardless of the resistance reduction determined, a clear interaction between longitudinal vortices near the plate and local contributions to flow resistance could be demonstrated. Since these longitudinal vortices are directly influenced by the dimples, it is very likely that an optimized arrangement of the dimples, adapted to the flow conditions, can reduce the resistance.
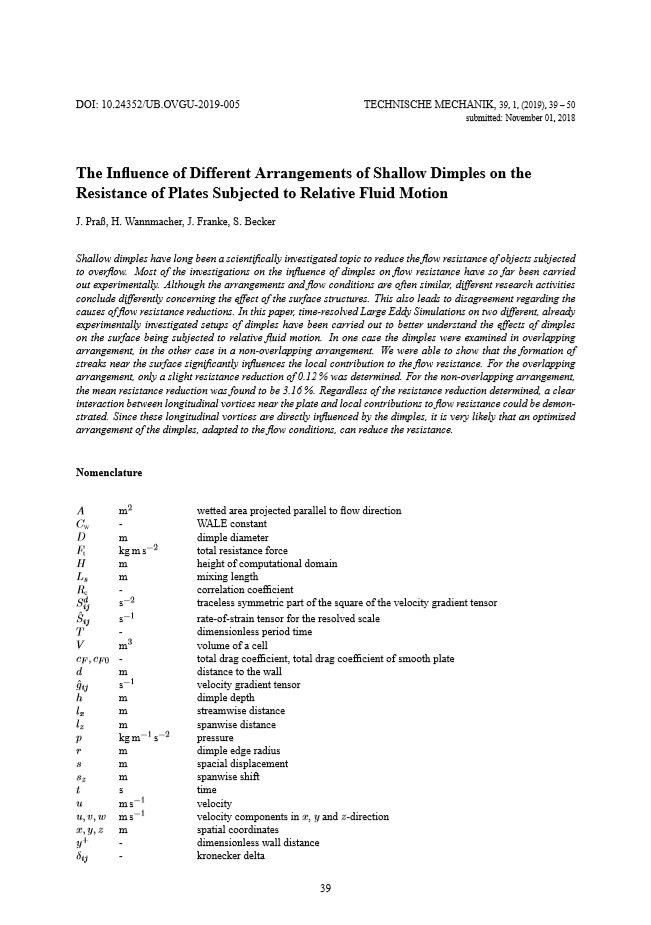