1D thermal modelling of a wheel bearing to investigate energy losses
DOI:
https://doi.org/10.24352/UB.OVGU-2023-047Keywords:
1D simulation, Heat transfer, Insulation, Thermal mass model, Wheel bearing, WLTP driving cycleAbstract
This paper presents the 1D thermal multi-mass simulation of a wheel bearing in order to estimate how the component
temperatures affect the energy loss during the Worldwide Harmonized Light Vehicles Test Cycle (WLTC). The simulation model
was developed in MATLAB/Simulink on the basis of the conductive and convective heat transfer equations. The ambient air and bearing components are represented by 7 simplified thermal mass points. The physical quantities necessary to create these points such as area, mass and material of the components were taken from the bearing’s 3D computer model. The heat transfer between the individual masses can be determined by setting different values of heat transfer coefficients. In this way it can be observed how much thermal insulation and proper material selection can improve the energy efficiency. The simulation model was created with speed, stability and robustness in mind in order to allow a level of accuracy that meets industrial and scientific expectations. To validate the model, the simulation results were compared to experimental data. A case study with different heat transfer parameters was concluded to quantify the effect of insulation and so, the energy saving potential.
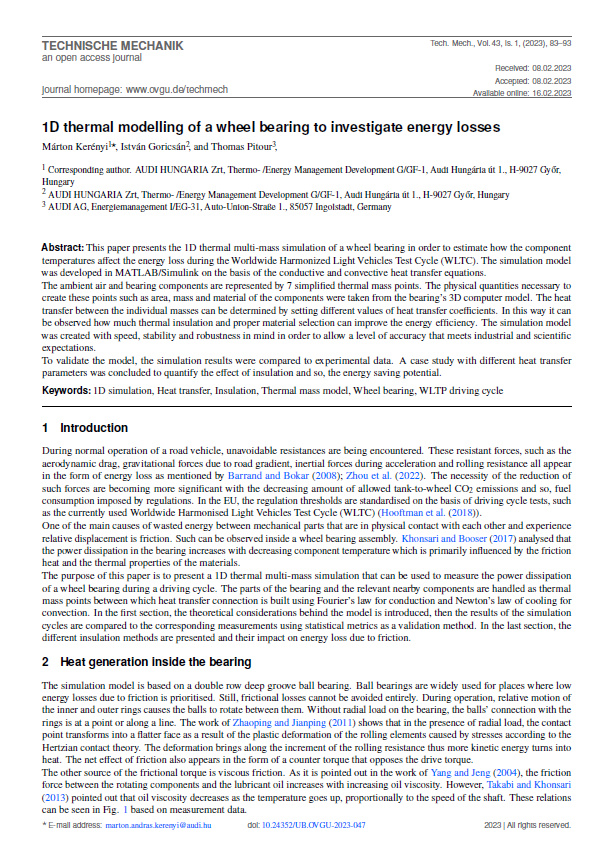
Downloads
Published
How to Cite
Issue
Section
License
Copyright (c) 2023 Márton Kerényi, István Goricsán, Thomas Pitour

This work is licensed under a Creative Commons Attribution-ShareAlike 4.0 International License.