Comparison of Numerical Forced Response Predictions with Experimental Results Obtained in a Subsonic Test Turbine Facility
DOI:
https://doi.org/10.24352/UB.OVGU-2017-091Abstract
In order to achieve the ACARE targets regarding reduction of emissions it is essential to reduce fuel consumption drastically. Reducing engine weight is supporting this target and one option to reduce weight is to reduce the overall engine length (shorter shafts, nacelle). However, to achieve a reduction of engine length the spacing between stator and rotor can be minimised, thus changing rotor blade excitation. Related to the axial spacing, a number of excitation mechanisms in respect to the rotor blading have to be considered already during the design process. Based on these facts several setups have been investigated at different engine relevant operating points and axial spacing between stator and rotor in the subsonic test turbine facility for aerodynamic, acoustic, and aeroelastic investigations (STTF- AAAI) at the Institute for Thermal Turbomachinery and Machine Dynamics at Graz University of Technology. In order to avoid upstream effects of supporting struts, these struts are far downstream of the stage which is under investigation. In this paper the capability to predict forced response vibrations of selected rotor blades is evaluated with experimental results for two different axial gaps between rotor blade and stator vane row. The investigation is done for engine relevant operating conditions. For rotor blade vibration measurements a novel telemetry system in combination with strain gauges is applied. The stage was modelled using the software package ANSYS. Flow fields up and downstream of the turbine stage are analysed and visualised for two axial gaps and compared to the forced response of the blading. Detailed structural dynamic investigations show critical modes during operation which are identified by the telemetry measurements as well. Finally, the influence of the axial spacing regarding the rotor blade excitation and vibration can be elaborated and is prepared to get a better understanding of basic mechanism. The paper shows that reducing axial spacing is a promising option when reducing engine weight. However, prediction of forced response vibrations is still challenging due to the variety of unknown parameters of a real life engine such as coupling stiffness, damping, blade mass, etc.
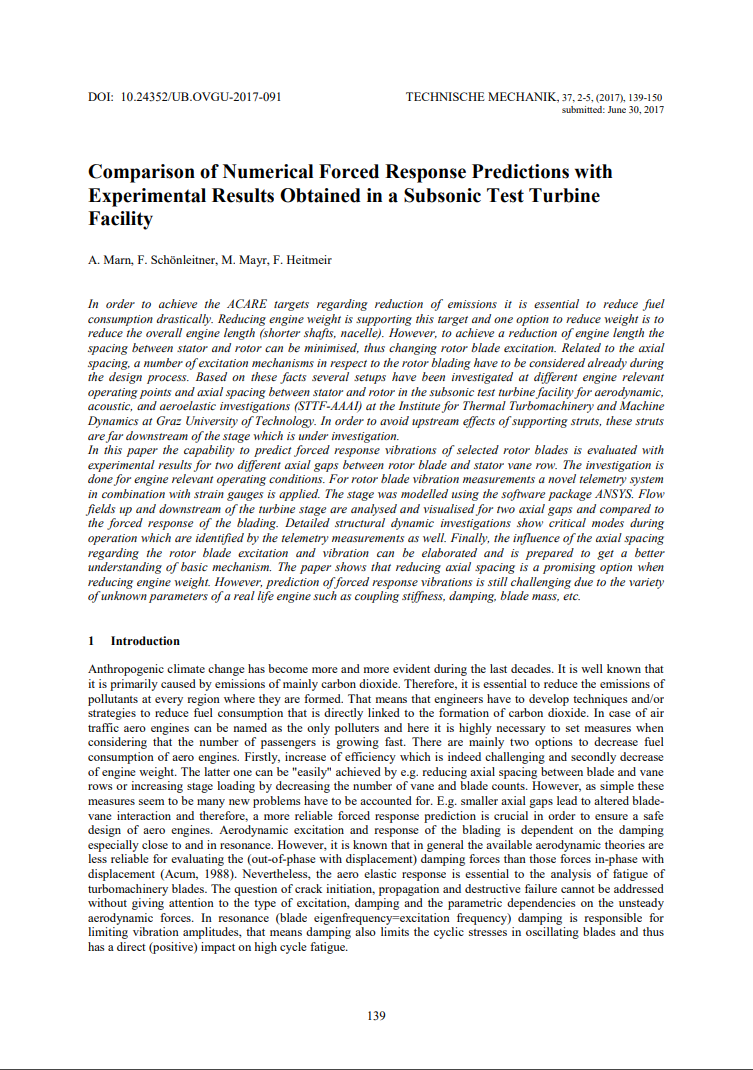