Turbocharger Dynamic Analysis
Advanced Design Simulation in Time Domain Using CFD Predicted Thermal Boundary Conditions
DOI:
https://doi.org/10.24352/UB.OVGU-2017-117Abstract
Small changes of surface temperature, clearance and bearing profile can significantly change stiffness and damping characteristics of slider bearings. This may influence dynamics and in case of turbochargers the rotor radial deflection. Noise, Vibration, Harshness (NVH) or durability issues like rotor colliding with housing may be implied as a consequence.
This paper presents a new methodology for dynamic turbocharger investigation. It considers multi-body dynamics (MBD) of flexible rotor and housing structures coupled with elasto-hydrodynamics (EHD) of the inner and outer oil film. The energy equation for calculation of oil film temperature is considered in EHD using hermal boundary condition obtained from 3D computational fluid dynamics (CFD) simulation. Typical targets for CFD simulation within the turbocharger development process are flow and thermal investigation as well as specifically providing accurate thermal boundary condition for thermo-mechanical fatigue analysis. For this purpose CFD analysis considers a fully coupled fluid-structure interaction. However, the same CFD model can be used to provide the required boundary conditions for dynamic analysis as well. The bearing profiles under thermal load are derived from Finite Element (FEM) analysis based on same thermal boundary conditions.
The authors demonstrate the application of the methodology for a typical turbocharger design study applied for heavy-duty engines with full floating bushings that have radial bore connections between inner and outer oil films. The rotor operating speed reaches up to 110 krpm. Dynamic simulation results with nominal clearance and temperature are compared with the results obtained when CFD and FEM predicted boundary conditions are used. Based on results for the oil film pressure and flow through each oil film as well as flow between inner and outer oil film a valid conclusion about the rotor dynamic behaviour, bearing mechanical and thermal loads can be made. The presented methodology proves to be a next level approach in prediction of turbocharger simulation in the development process.
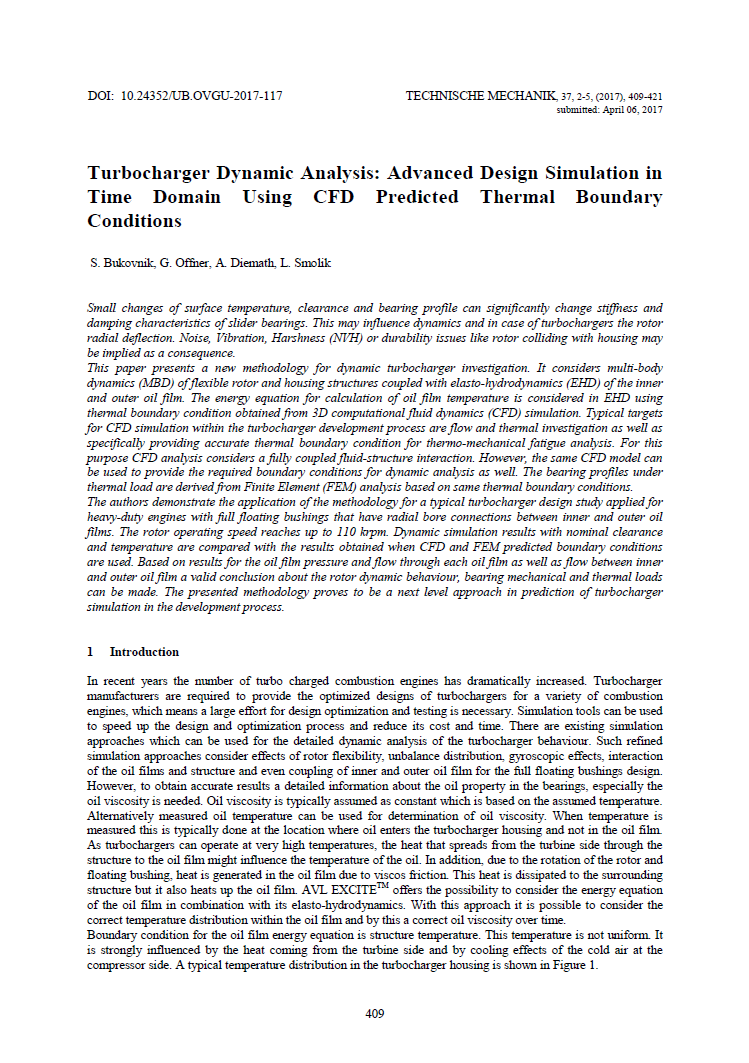