Vibration Signal Analysis for the Lifetime-Prediction and Failure Detection of Future Turbofan Components
DOI:
https://doi.org/10.24352/UB.OVGU-2017-118Abstract
Planetary gearbox and hydrodynamic journal bearings (HJB) are going to be integrated in future turbofan engines. This paper presents the results of applied methods to detect failures of these components. At first, failure detection requirements are derived by using system engineering techniques. In consideration of the identified failures theoretical assumptions are discussed and subsequently verified. Vibration and acoustic emission (AE) sensors seem promising to detect failures in an early stage. To prove the theoretical considerations experiments are carried out on test benches.
Tooth flank damage of a planet gear in a planetary gearbox design is investigated. High demands are placed on the signal processing due to design-related amplitude modulation effects. Vibrations are measured using acceleration and AE sensors, which are mounted on the ring gear. The investigated failure type leads to excitation of non-stationary AE signals. It is proposed that the AE signals have a cyclostationary characteristic. Using cyclostationary-based processing techniques the signal’s hidden periodicities can be revealed. A separated analysis of each planet and evaluation of the envelope spectrum finally allows the detection of this failure type.
Instead of roller bearings, HJB can be integrated in planet gears. The most essential damaging mechanism for HJB is wear as a result of mixed or boundary friction. These friction states are caused by conditions like Start/Stop Cycles, insufficient oil supply, overload or oil contamination. The accumulated intensity and duration of friction can be a measure of the remaining useful lifetime (RUL). To estimate the RUL friction has to be differentiated regarding the intensity. AE technology is a promising method to detect friction in HJB.
Therefore, AE signals of the mentioned conditions are acquired. Due to rotating planet gears there is no possibility to place AE sensors directly on the surface of HJB. Finally suitable features for both components are extracted from the processed signals. Their separation efficiency with respect to the failure types is evaluated.
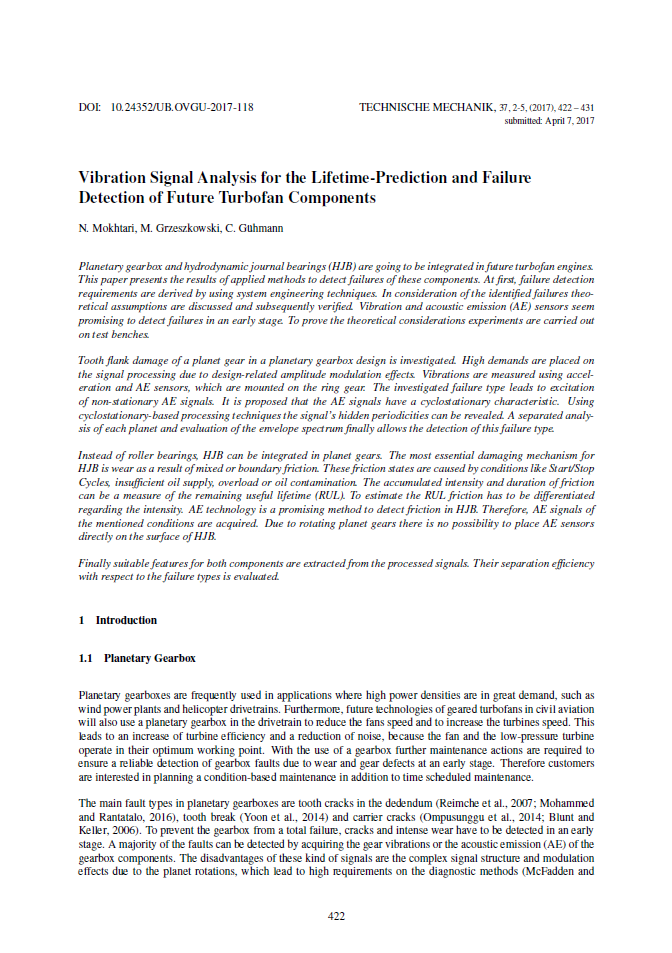