Constitutive Modelling of Superplastic AA-5083
Abstract
In this study a fast procedure for determining the constants of superplastic 5083 Al alloy at 723 K is analyzed. To evaluate the displacement and the thickness evolutions at the dome apex of the metal sheet bulge forming experiments at constant pressure are performed. The displacement-time curves at the constant pressures of 0.30, 0.35, 0.40, 0.45 and 0.50 MPa are obtained by laser measurements whereas many bulging tests at the same gas pressures stopped up at prefixed intervals of time were carried out to evaluate the thickness at the dome apex. Direct measurements of the thickness were obtained using a centesimal micrometer. It is known that an equibiaxial stress state is present at the dome apex of the metal sheet. In contrast, at other locations, a nonequibiaxial stress state prevails. Due to the nonequibiaxial stress state, the thickest location occurs at the sheet periphery and the thinnest location at the dome apex. Therefore, by using the finite element method, it is possible to accurately analyse the superplastic forming process in the real stress state conditions. The material behaviour is modelled by the power law relationship between the effective flow stress, the effective strain and the effective strain-rate. In the power law relationship the strain-rate sensitivity index, m, is a constant, n and K are variables that are functions of the effective strain-rate. Experimental results allowed to easily determine the value of m. Moreover, by means of some numerical simulations it was possible to determine the values of n and K and associate them with specific strain-rates. The results of comparison of the numerical simulations of a bulge forming process with the experimental tests have shown good agreement and they indicate that the material constants are reliable.
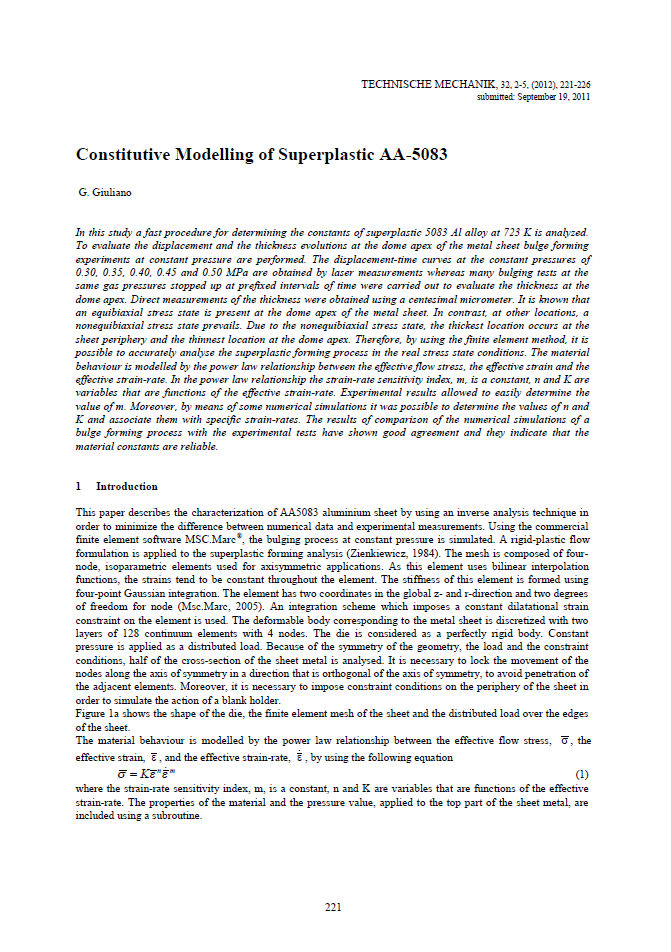