Modelling Ultra High Pressure Compaction of Powder
Abstract
The use of high pressure high temperature (HPHT) equipment varies; in mineral physics research the equipment is used for investigation of the earth’s interior and in industry it is used for commercially produced synthetic diamonds and other polycrystalline products. The common denominator for almost all high pressure systems is to use capsules where a powder material encloses the core material. Numerical analysis of the manufacturing processes with working conditions which reaches ultra high pressure (above 10 GPa) requires a constitutive model which can handle the specific behaviours of the powder from a low density to solid state. Calcium carbonate (CaCO3) is a mineral that can be used in high pressure processes and is very common in the earth core. A constitutive model for calcium carbonate applied to high pressure compaction is presented. The plastic response of powder is non-linear and described in a rate-independent cap plasticity model. The cap model has been developed to capture the behaviour of minerals in high pressure applications. The yield function consists of a failure envelope fitted to a strain-hardening cap. Experimental tests with a Bridgman anvil set-up using calcium carbonate powder discs are performed. Numerical analysis using the finite element method is done to virtually reproduce the experiments. Results from the analysis are compared to measured experimental results. The numerical analyses agree reasonably well with the experimental results.
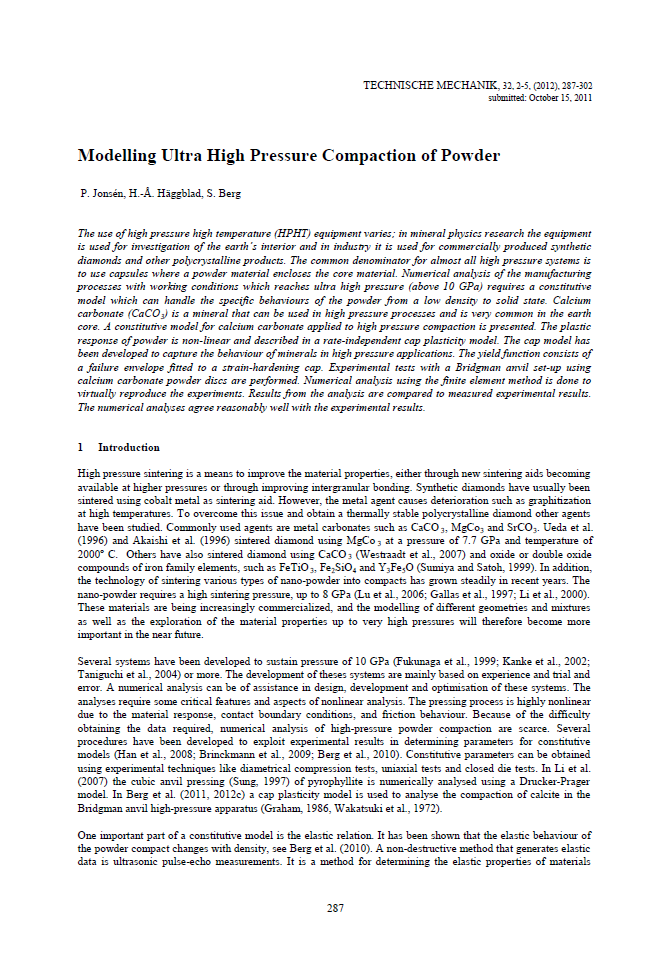