A Mechanism-Based Approach to Life Prediction for a Nickel-Base Alloy subjected to Cyclic and Creep-Fatigue
Abstract
A large number of damage parameters have been proposed to estimate cyclic fatigue life predominantly at ambient temperatures. However, especially in aerospace and automotive industry fatigue models with a wide temperature application range are required. Here, the regimes of high temperature creep-fatigue and nonisothermal thermo-mechanical fatigue are of particular interest.
Within the present work a new mechanism-based life prediction approach is proposed for a nickel-base superalloy. The ability of the model to describe fatigue at low, intermediate, and also at high temperatures is investigated. Isothermal, as well as non-isothermal loading conditions are considered. The enhanced model formulation is based on the micro crack growth parameter Z d introduced by Heitmann et al. (1984). The model incorporates a threshold concept and corrections for mean stress and creep effects. In addition the detrimental effects caused by oxygen-induced embrittlement of the near tip region are accounted for by a parabolic oxidation approach. Test data from literature is used to compare the proposed model to several other fatigue models. Basis for all life prediction approaches under investigation is the stress-strain response of the material obtained by finite element analysis. Therefore, an inelastic constitutive model is applied. The fatigue model accuracy is evaluated on a statistical basis through an evaluation of the variance in the ratio of predicted life to actual life. This is done for the entire test database as well as for subsets, like isothermal, thermo-mechanical, and dwell tests only.
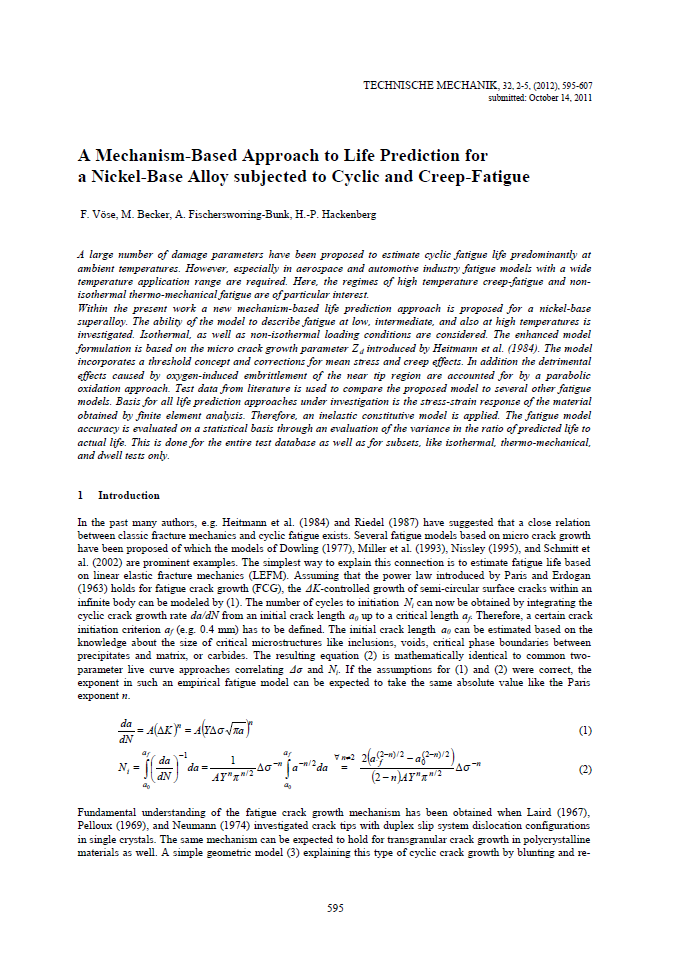