A three-dimensional model for stage I-crack propagation
Abstract
The propagation of short fatigue cracks is simulated by means of a three-dimensional model. Under loading conditions in the high cycle fatigue regime the growth of these cracks can determine up to 90% of the lifetime of a component. Stage I-cracks often grow on slip bands and exhibit strong interactions with microstructural features such as grain boundaries. Experimental investigations have shown that the crack propagation rate decreases significantly when the crack tip approaches a grain boundary and even a complete stop of crack propagation is possible. In order to consider the real three-dimensional orientation of a slip plane an existing two-dimensional mechanism-based model (Künkler el al., 2008) is extended to simulate the propagation of a three-dimensional surface crack. The crack geometry is modelled using dislocation loops (Hills et al., 1996), which represent the relative displacement between the crack flanks. To describe the propagation of stage Icracks elastic-plastic material behaviour is considered by allowing a plastic deformation due to slip on the active slip plane. The extension of the plastic zone is blocked by the grain boundary. The crack propagation law is based on the range of the crack tip slide displacement, which is obtained from the plastic solution. Behind the grain boundary the shear stress field is evaluated. Results show that a high twist angle between the slip planes causes a significant decrease in the stresses, which can yield a crack stop.
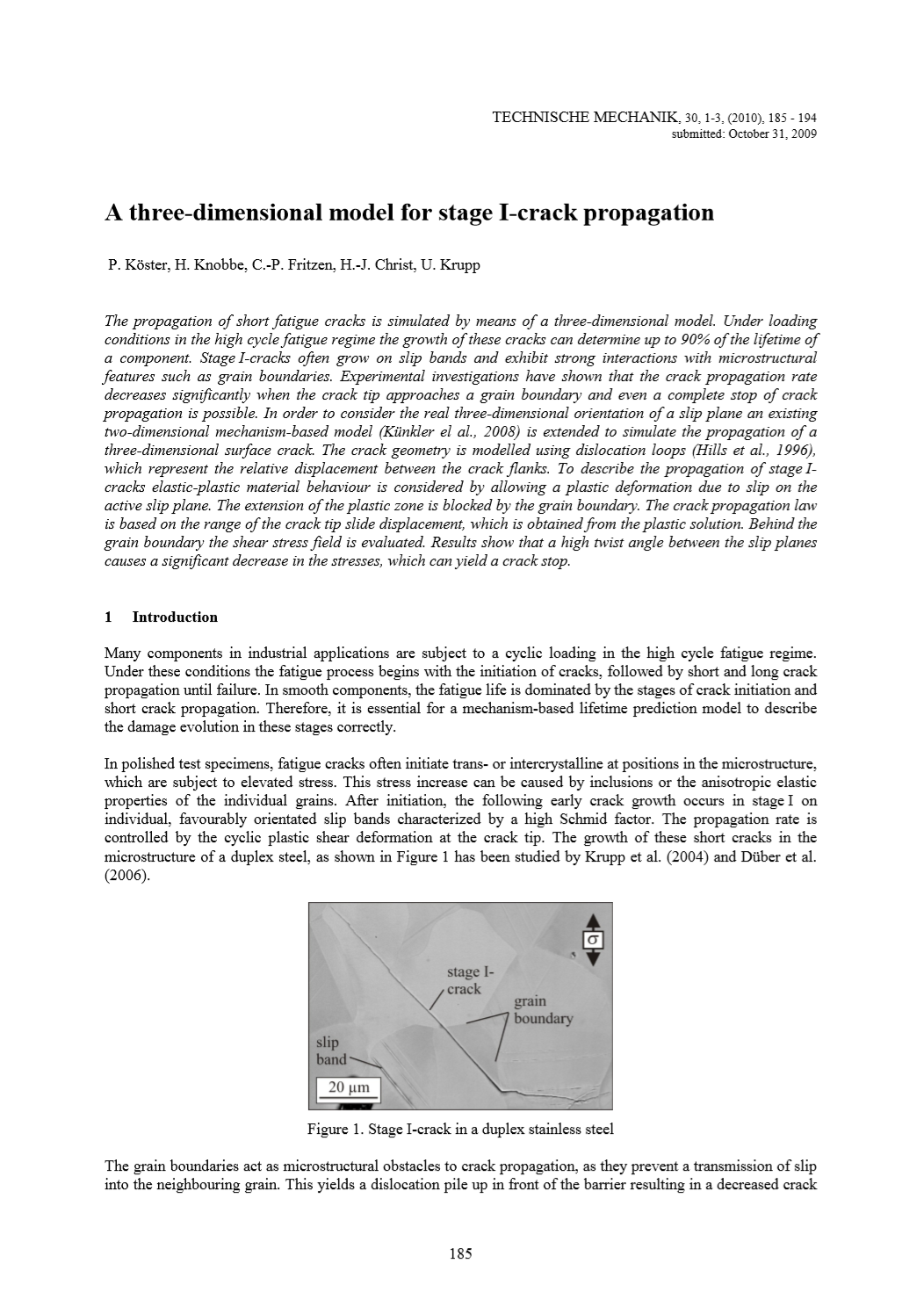