Modeling Silicon under Contact Loading Conditions
Aspects of Non-Associated Flow
Abstract
Technologically relevant abrasive machining techniques (lapping, sawing, grinding) for silicon (Si) are based on (sub-)surface crack formation triggered by contact events. Therefore, the understanding of the inelastic deformation of Si under contact (indenter-)loading is essential to improve machining results. It has been long established that Si undergoes a series of stress driven phase transitions under compression. During subsequent pressure release part of the transformation strain is recovered. The present paper highlights the importance of the direction of inelastic flow for modeling (partially) reversible stress induced phase transitions in materials such as silicon. A phenomenological constitutive model for Si under contact loading, which captures both the cd−Si → −Si transition upon compression and the −Si → a−Si transition upon rapid decompression has been recently presented (Budnitzki and Kuna, 2012). It is shown that indentation experiments are particularly well suited to determine material parameters for this model. Further, material parameters obtained from indentation experiments with Berkovich indenter are confirmed to be valid for the numerical simulation of Knoop indentation, thus verifying a certain predictive capability of the constitutive model.
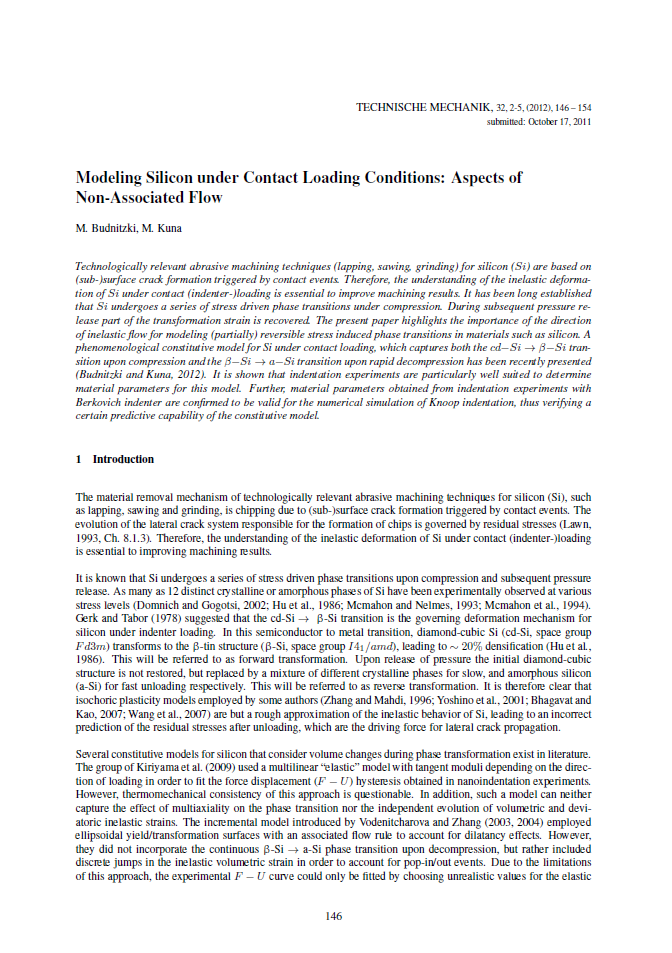