A Microstructure Sensitive Approach for the Prediction of the Creep Behaviour and Life under Complex Loading Paths
Abstract
The prediction of the creep behaviour and life of components of aeronautic engines like high pressure turbine blades is still a challenging issue due to non-isothermal loadings. Indeed, certification procedures of turboshaft engines for helicopters consist of complex thermomechanical histories, sometimes including short and very high temperature excursions close to the γ’-solvus (T~1200°C) of the blade alloy. A better design of those components could be gained using a model that takes into account non-isothermal loadings inducing microstructural changes.
Most of the commonly used models consider only a nearly constant (or slowly evolving) microstructure, i.e. far from the rapid microstructure evolutions encountered during close γ’-solvus overheatings where a rapid dissolution/precipitation of the γ’-phase and fast recovery mechanisms were observed by Cormier et al. (2007b). A new constitutive modelling approach was hence recently proposed in a crystal viscoplasticity framework to capture the transient effects of such rapid microstructure evolutions on the creep behaviour and life (Cormier and Cailletaud (2010a)).
In this article, an updated version of this model is detailed. Special attention will be paid to (i) the effect of the accumulated plastic strain on the microstructure evolution, (ii) the introduction of an additional damage formulation, and (iii) the creep strain at failure. The performances of the model are illustrated on the basis of isothermal or complex non-isothermal creep experiments performed on nearly [001] oriented samples.
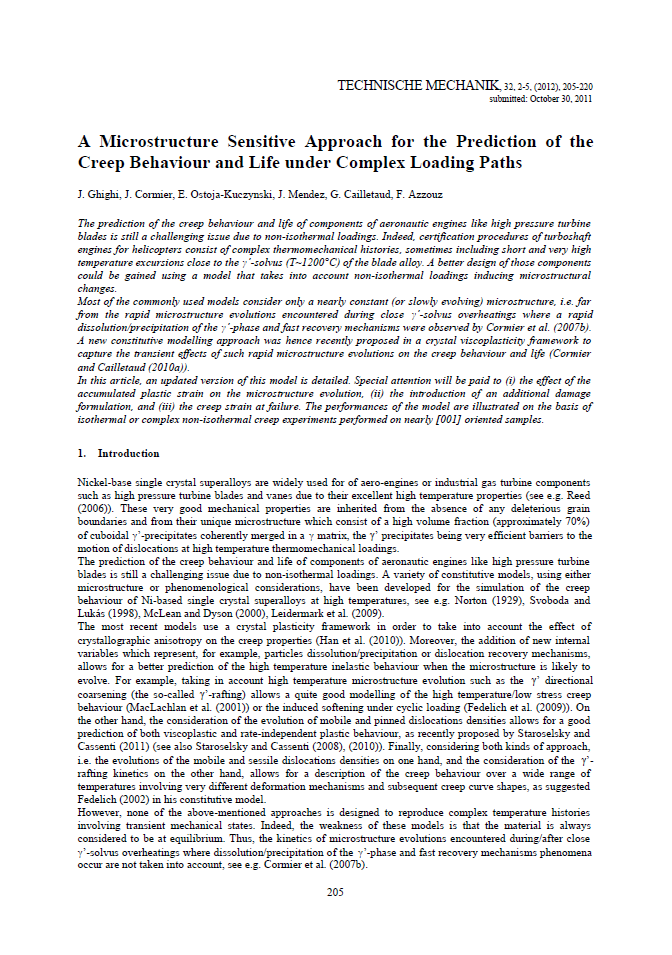