Constitutive modelling of the creep behaviour of single crystal superalloys under non-isothermal conditions inducing phase transformations
Abstract
The prediction of the viscoplastic behaviour of Ni-based single crystal superalloy is still a challenging issue due to the non-isothermal loadings which can be encountered by aeronautic engines components such as high pressure turbine blades and vanes. Under particular in-service conditions, these materials may experience temperature cycles which promote the dissolution of the strengthening g’-phase of the material on (over)heating, and subsequent precipitation on cooling, leading to a transient viscoplastic behaviour. New internal variables representing the microstructural changes under those specific thermal loadings have been introduced in the framework of crystal plasticity using a macroscopic approach (no representation of the g/g’ microstructure of the alloy) to account for the transient creep behaviour induced by microstructure changes. This modelling approach captures first order effects on the creep behaviour due to (a) g’ precipitates volume fraction evolution of each kind of particles of a bimodal distribution of precipitates (which evolves according to thermal history), (b) recovery of the dislocation density and, (c) material orientation. In addition, a damage law keeping in memory all the thermal history and recovery processes has been introduced to account for the unconventional post-overheating creep life. This model is calibrated on non-isothermal creep experiments on [001] oriented single crystals made of MC2 alloy. It is able to predict creep strain (primary, secondary, tertiary), whatever the temperature history of the material.
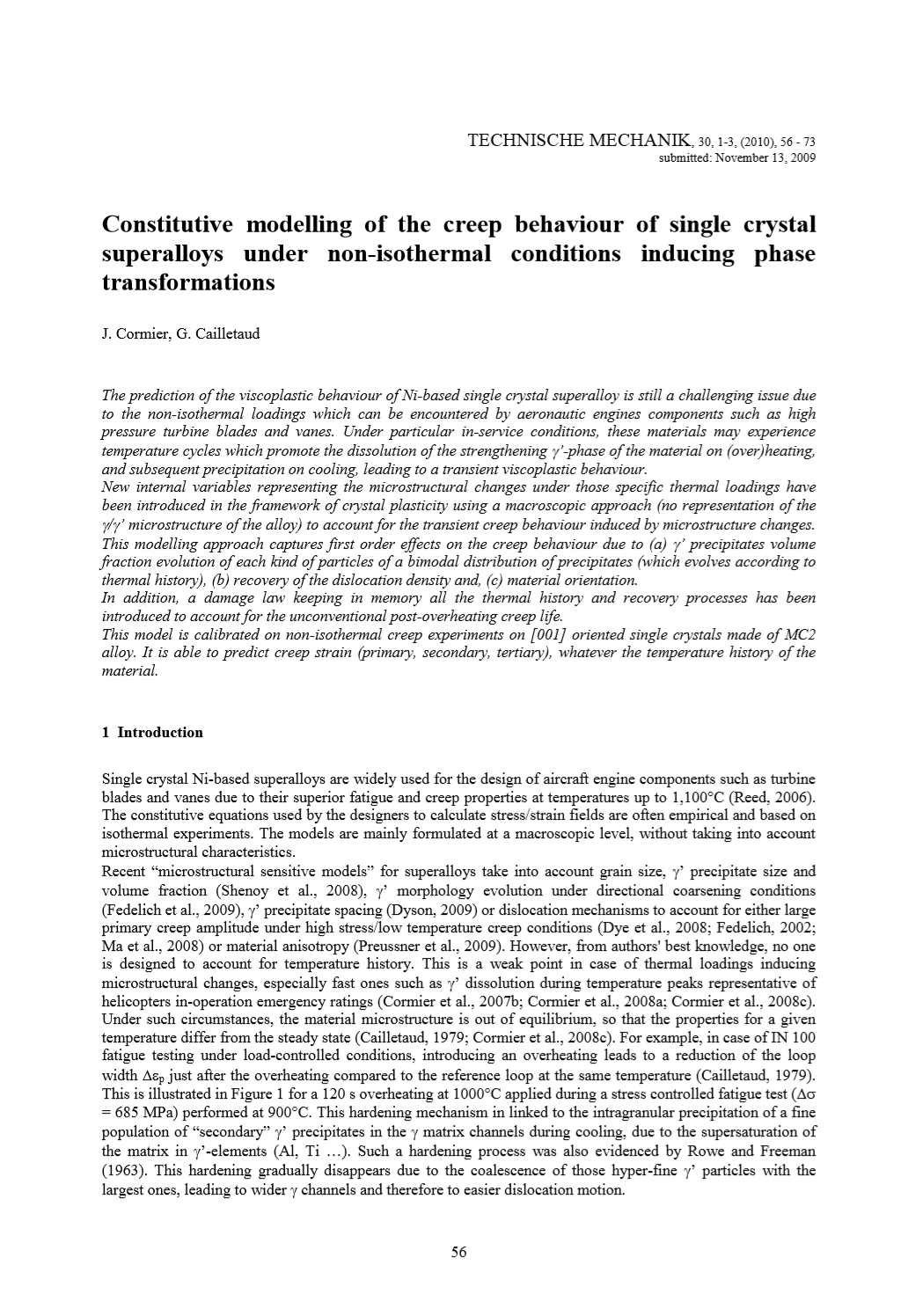