Computational Homogenisation of Polycrystalline Elastoplastic Microstructures at Finite Deformation
Abstract
During sheet bulk metal forming processes, both flat geometries and three-dimensional structures change their shape while undergoing large plastic deformations. As for metal forming processes, FE-simulations are often done before in-situ experiments, a very accurate model for respective structures is required, performing well at small geometries possessing small curvatures as forms with wide as well as lateral characteristics.
Because of the crystalline nature of metals, certain anisotropies have to be taken into account. Macroscopically observable plastic deformation is traced back to dislocations within considered slip systems in the crystals causing plastic anisotropy on the microscopic and the macroscopic level.
A crystal plasticity model for finite deformations is used to model the behaviour of polycrystalline materials in representative volume elements (RVEs) on the microstructure. In order to circumvent singularities stemming from the linear dependency of the slip system vectors, a viscoplastic power-law is introduced providing the evolution of the plastic slips and slip resistances. The model is validated with experimental microstructural data under deformation. Through homogenisation and optimisation techniques, effective stress-strain curves are determined and can be compared to results from real forming processes, leading to an effective elastoplastic material model which is suitable for processes in the sheet bulk metal forming field.
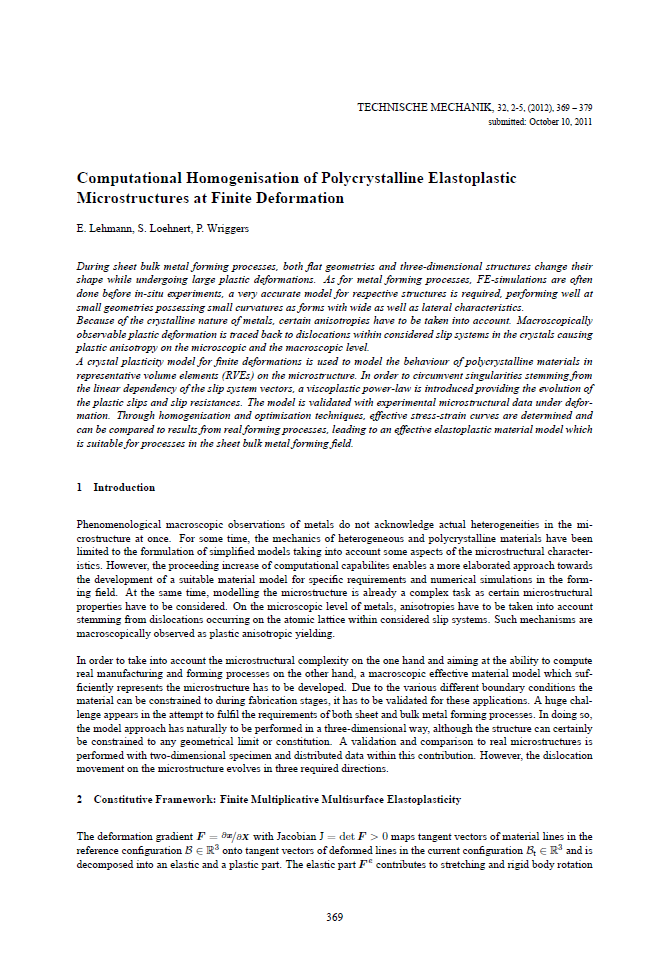