Development of a thermomechanically coupled damage approach for modeling woven ceramic matrix composites
DOI:
https://doi.org/10.24352/UB.OVGU-2020-014Keywords:
CMC, RVE, cohesive zone, continuum damage, composites, wovenAbstract
Ceramic matrix composites (CMCs) as an enhancement of classical technical ceramics overcome limitations such as low fracture toughness and brittle failure under mechanical or thermomechanical loading. Their low weight and high temperature stability makes them attractive for use in various fields, especially aerospace industry, where they improve engine efficiency as substitutions for metal components. Despite their positive attributes current CMCs lack well established material property design databases for a reliable use in critical aerospace structures. Demonstrating the durability and lifespan of this relatively new class of materials is the present task. Therefore their failure mechanisms need to be investigated further, taking into account the extensive range of temperatures the components are subjected to. This contribution deals with the successive development of a woven representative volume element (RVE) for arbitrary CMCs. In contrast to previously developed approaches, the introduced model combines various damage formulations. The fiber bridging effect is governed using a cohesive zone (CZ) formulation to adress the debonding mechanism in the weak interface between matrix and reinforcement and a continuum mechanical approach to account for matrix damage. To cover the temperature dependency of the material parameters, thermal coupling is included in both element formulations.
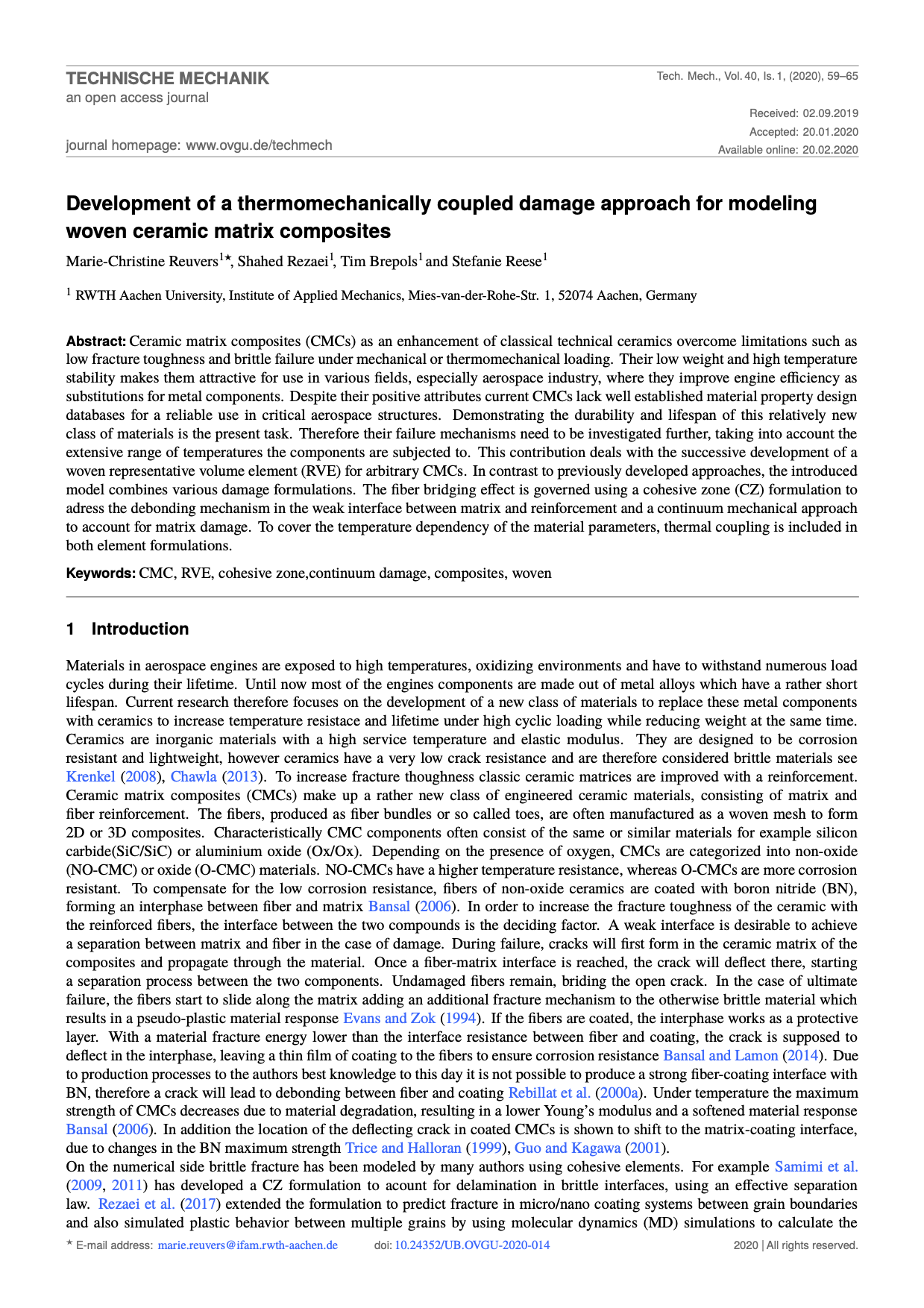