Modeling of hyperelastic material accounting for the Mullins effect by defining a new stiffness reduction variable
DOI:
https://doi.org/10.24352/UB.OVGU-2020-016Keywords:
rubberlike material, hyperelasticity, Mullins effect, silicone adhesives, continuum damage mechanics, finite strainsAbstract
Supporting structures in the field of glass façade construction are increasingly relying on making use of silicone adhesives. Hence, predicting the hyperelastic behavior and the stiffness reduction (Mullins effect) of such adhesives is essential for the economical dimensioning of load-bearing bonds. For this, a phenomenological hyperelastic model at finite strains is defined, which enables an accurate prediction of the real material behavior. The presented model is based on the Ogden model. Two internal variables are defined, which describe stiffness reduction during loading and unloading procedures and hardening or softening behavior, to model the experimentally observed behavior. For the calibration of the corresponding material parameters, a staggered parameter identification scheme is proposed in order to obtain a unique parameter set for the representation of multiaxial stress states. The excellent model prediction is shown by selected examples.
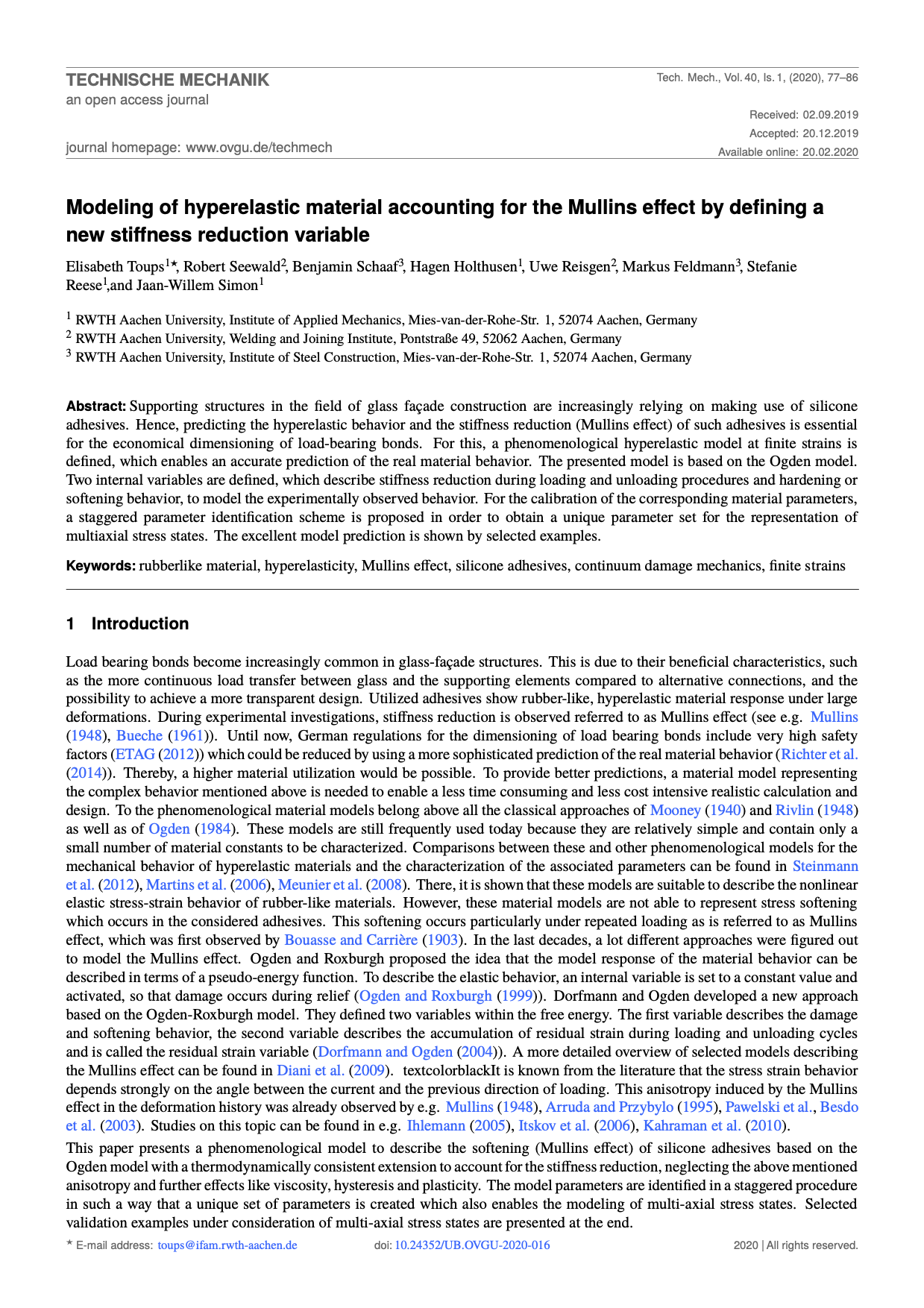