Analysis of Processes with Axisymmetric Plastik Flow of Metals
Abstract
A numerical method for the analysis of stresses and plastic flow rates is presented for processes with axisymmetric plastic flow of metals. This techniques is based on a representation of yield zones in a special formulation of the stresses related to Iljushin's deviatoric stress space. The basic differential equations describing axisymmetric plastic flow are solved by hyperbolic approximations. In fact, the approach represents an enhanced method of slip lines since the characteristics of the differential equations for stresses and rates coincide with these. This condition is very important for the analysis of damage induced by voids which generate microscopic slip bands. The method is illustrated by an analysis of the forging process of an axisymmetric part made of low-carbon low-alloy steel. The stepwise analysis of deformation allows for calculating the contact load applied to the working tool, the strains accumulated within the part volume, and some "meso-parameters," e.g., the damage induced by strain micro-defects and the internal energy of hardening. Two integral measures connected with the hydrostatic and deviatoric parts of the damage tensor are used for the calculation of strain-induced damage. The predicted damage is significantly less than its permissible value, as high hydrostatic pressure in the plastic zone heals micro-defects, prevents their growth, and, thereby, increases the processing ductility of deformed metals during forging. The research results allow us to give some recommendations for the selection of appropriate processing strains for forging in order to achieve high strength properties of the produced axisymmetric case-shaped parts.
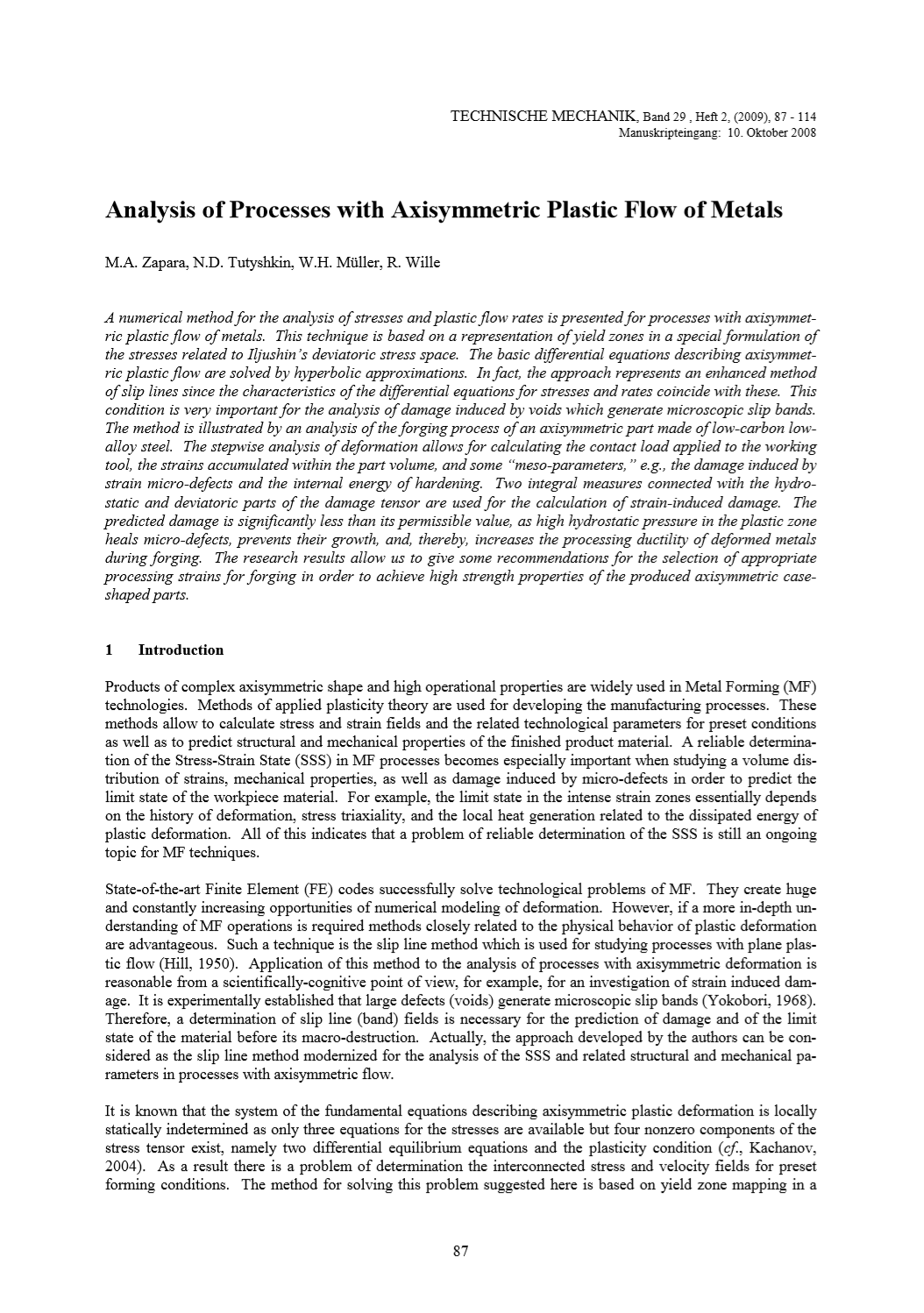